Going the Extra Mile to Deliver for Our Consumers
Keurig Dr Pepper has been in the incredibly fortunate position that demand for our product remained strong, even increasing in certain categories, throughout the pandemic. Our teams rose to the occasion, going above and beyond to get our products out as demand continues to grow.
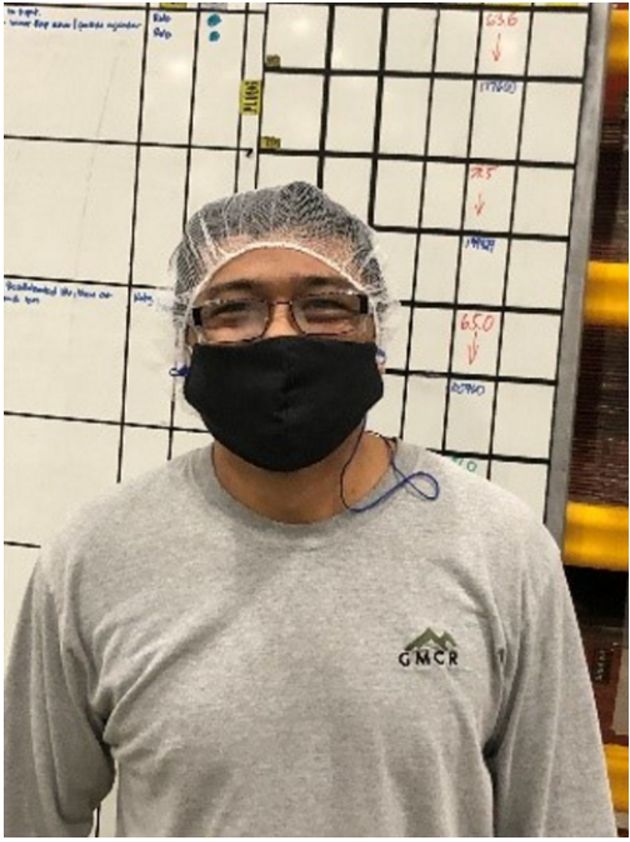
At the beginning of the pandemic, Keurig Dr Pepper lab technicians had to get creative in order to keep up with increased consumer demand. Technicians out of our Burlington, Massachusetts pod quality lab, Brian and Evan, volunteered to come back to work after the building was closed. They completed qualification testing for two new suppliers needed to provide raw materials to prevent any disruption to production. The quality team worked with the facilities team to ensure safe operations during this time.
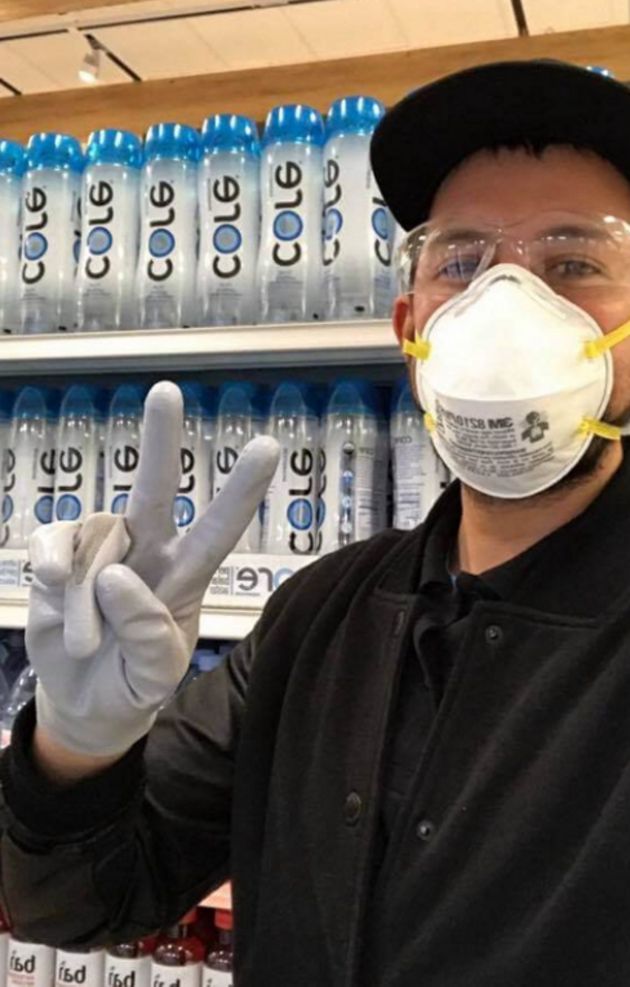
Our direct-store-delivery team has also continued to go above and beyond during these unprecedented times. In Las Vegas, Nevada, team members Jesus, Operations Supervisor, Eric, Inventory Coordinator, and Roxanna, Operations Manager, each drove ten hours on a Saturday after an exceptionally busy work week to fulfill a need to pick up product in Vernon, California. With quick support from Vernon forklift operators, they loaded up and got back to Las Vegas to ensure customers’ orders were fulfilled on time.
To note another example, Dennis, a product technician at the Sumner, Washington, manufacturing plant, stepped up when his team needed help. He ran an entire production line on his own, maintaining 80% operating efficiency while producing hundreds of thousands K-Cup pods, only stopping for breaks and lunch. Due to Dennis’s commitment to excellence, the line was able to stay running and complete an additional boost to production.
Our direct-store-delivery team has also continued to go above and beyond during these unprecedented times. In Las Vegas, Nevada, team members Jesus, Operations Supervisor, Eric, Inventory Coordinator, and Roxanna, Operations Manager, each drove ten hours on a Saturday after an exceptionally busy work week to fulfill a need to pick up product in Vernon, California. With quick support from Vernon forklift operators, they loaded up and got back to Las Vegas to ensure customers’ orders were fulfilled on time.
To note another example, Dennis, a product technician at the Sumner, Washington, manufacturing plant, stepped up when his team needed help. He ran an entire production line on his own, maintaining 80% operating efficiency while producing hundreds of thousands K-Cup pods, only stopping for breaks and lunch. Due to Dennis’s commitment to excellence, the line was able to stay running and complete an additional boost to production.
Our direct-store-delivery team has also continued to go above and beyond during these unprecedented times. In Las Vegas, Nevada, team members Jesus, Operations Supervisor, Eric, Inventory Coordinator, and Roxanna, Operations Manager, each drove ten hours on a Saturday after an exceptionally busy work week to fulfill a need to pick up product in Vernon, California. With quick support from Vernon forklift operators, they loaded up and got back to Las Vegas to ensure customers’ orders were fulfilled on time.
To note another example, Dennis, a product technician at the Sumner, Washington, manufacturing plant, stepped up when his team needed help. He ran an entire production line on his own, maintaining 80% operating efficiency while producing hundreds of thousands K-Cup pods, only stopping for breaks and lunch. Due to Dennis’s commitment to excellence, the line was able to stay running and complete an additional boost to production.